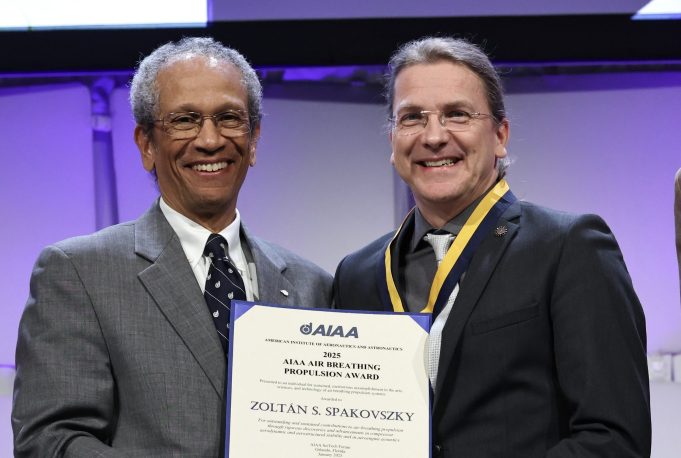
Professor Zoltán S. Spakovszky receives the 2025 AIAA Air Breathing Propulsion Award
The American Institute of Aeronautics and Astronautics (AIAA) has selected Zoltán S. Spakovszky as the recipient of the 2025 AIAA Air Breathing Propulsion Award. This award is presented for outstanding and sustained contributions to air-breathing propulsion through rigorous discoveries and advancements in compressor aerodynamic and aerostructural stability and in aeroengine acoustics.
Prof Spakovsky will be presented with the award during the AIAA Awards Recognition Ceremony, on Monday, January 6 at the 2025 AIAA SciTech Forum.
From his nomination:
“Professor Spakovszky is internationally recognized for contributions in unsteady flows in aeropropulsion, including the aerodynamic and aerostructural instabilities that are endemic to aeroengines, the aeroacoustics of jet engines and aircraft, and aerospace dynamical systems for a range of different applications. His research, aimed at satisfying the demand for safer, more efficient, and quieter turbomachinery for air transportation, spans a broad spectrum of topics: compressor fluid mechanics and stability, compressor and turbine rotordynamics, conceptual design of innovative aircraft and gas turbine propulsion systems, bearings for micro-turbomachinery, and aircraft noise reduction.
His work is characterized by a passion for solving complex, real world, technologically relevant problems, in a rigorous and scientific manner. The research he conducts is marked by the depth and breadth of the topics covered, the intellectual level of problem engagement, the ties to industry problems, and to his capabilities in striking out in new directions in our field.
Some of Prof. Spakovszky’s notable research accomplishments:
- Engine Deterioration & Aerodynamically Induced Compressor Whirl in Aeroengines: a first-of-a-kind analysis of aeroengine instability during accelerations, confirming the mechanism for acoustic resonance seen in roughly 360 aircraft engines in service.
- Criterion for Axial Compressor Hub-Corner Stall Development: a new, physical mechanism-based criterion for three-dimensional hub-corner stall in axial compressors, a key to loss production and to compressor stability.
- Surge Diagnostics & Control in Advanced Turbocharger Compressors Prediction: Measurement and explanation of new phenomenon in industrial centrifugal compressors that linked dynamic stability and coupling effects in unsteady swirling flows.
- Micro Fluidics – High-Speed Micro Gas Bearings: Spakovsky designed novel, low aspect ratio, low Reynolds number, hydrostatic gas bearings, and developed a new theory for micro-gas bearing dynamic behavior and a first-of-a-kind criterion for whirl instability.
- Aero-Acoustics – Novel Engine Airbrake for Quiet Aircraft: a novel device to generate quiet aircraft drag, using swirling engine exhaust flows to promote drag forces from radial pressure gradients.
- Advanced Propfan Systems for Reduced Environmental Impact: First quantification of noise mechanisms using high-fidelity simulations combined with acoustic analogy.
- Turbomachinery Noise Shielding & Propulsion System Integration: delivered conceptual aerodynamic design, (based on the Silent Aircraft Initiative, for which Prof. Spakovszky was co-Chief Engineer) of low noise, low fuel-burn cargo aircraft to Boeing – N2A and N2B a/c used by NASA.
- Multiple-Pure Tone Noise in Advanced Inlet Systems: a novel method for bridging the gap between acoustics and aerodynamics, including simultaneous inlet distortion transfer, acoustic source noise, and non-linear propagation of rotor shock noise.
- Effects of Manufacturing Processes on Performance (Efficiency) of Composite Turbofan Blading: determined effect of manufacturing processes (surface waviness) on laminar-turbulent boundary layer transition in composite fans critical for higher bypass and engine efficiency.
Recently, Prof. Spakovszky has led a collaborative university-industry project aimed at the design, development, and operation of a technology demonstrator for a megawatt class integrated motor drive to power a civil aircraft. The project team comprises university faculty from propulsion, materials and additive manufacturing, aircraft aerodynamics, electrical power, and controls and systems, as well as industry participation. The aim is demonstration of a one megawatt integrated motor drive that exceeds the NASA 2030 goals. This project is being presented in a special session at the 2023 AIAA AVIATION/EATS conference.”