History
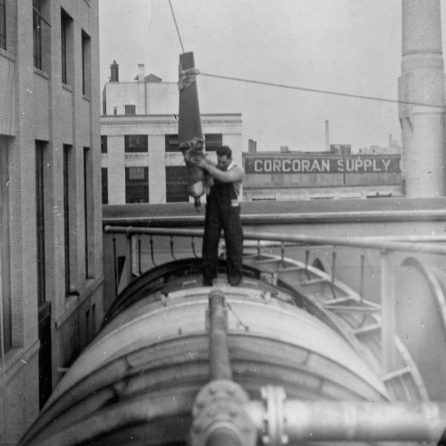
The Wright Brothers Wind Tunnel was dedicated on September 12, 1938, at the 5th International Congress of Applied Mechanics. It was named after Orville and Wilbur Wright to commemorate and perpetuate the research and controlled experimentation methods used to develop the first successful airplane. Initially, the tunnel was used for aerodynamic research on scale models of aircraft and their components, but later research focused on scale models of architectural structures. MIT built the Wright Brothers Wind Tunnel to replace the existing 4-foot, 5-foot, and 7.5-foot diameter wind tunnels, which had become virtually obsolete due to advances in the speed and size of aircraft. The Wright Brothers Wind Tunnel was utilized primarily by the aircraft manufacturing industry, which until the post-World War II period possessed few adequate wind tunnel facilities.
The original facility for the Wright Brothers Wind Tunnel represented state-of-the-art wind tunnel design and construction for its time. It was a closed-return, variable-density wind tunnel with a 7.5-foot by 10-foot diameter elliptical test section. Over the next 15 years, similar wind tunnel facilities cropped up around the U.S., but as aircraft design methods became more advanced, it eliminated much of the need for wind tunnel testing. With the advent of jet propulsion, a demand developed to test the aerodynamic characteristics of jet aircraft as they approached — and then surpassed — the speed of sound. To fill this void, the Wright Brothers Wind Tunnel staff designed the Blowdown Wind Tunnel, which was used from 1952 to 1959. Using interchangeable test sections and the Wright Brothers Wind Tunnel as a pressure reservoir, the Blowdown Wind Tunnel could run as either a transonic or supersonic wind tunnel. The aircraft industry and government agencies began to request testing time in the new facilities. Among those who used MIT’s “new” wind tunnel facility was the United States Air Force’s Office of Air Research, which investigated aerodynamics, aeroelasticity, and stability problems in the transonic speed range.
Although used primarily for aerodynamic tests of aircraft, the Wright Brothers Wind Tunnel was used for other purposes. In the late 1950s, the tunnel was used for numerous studies of the effects of wind on architectural structures and their environments, including Associated Universities, Inc.’s proposed radio telescope (1957), the Millstone Hill parabolic scanner (1957), the Green Building in MIT’s Eastman Court (1965), MIT’s Center for Advanced Engineering Studies (1966), and the Northeast Radio Observatory Corporation’s proposed radome (1966).
In the early 1960s, as U.S. government agencies and the aircraft manufacturing industry developed their wind tunnel facilities, the use of the Wright Brothers Wind Tunnel for aerodynamic research declined. Since then, it has been used primarily for studies of architectural structures and for MIT’s Department of Aeronautics and Astronautics student research projects.
A History of MIT Wind Tunnels
In 1896, Albert J. Wells built the first wind tunnel at MIT as part of his Mechanical Engineering thesis — a three-foot diameter square wind tunnel. In 1914, Jerome C. Hunsaker of MIT’s Department of Naval Architecture and Marine Engineering built a 4-foot diameter square wind tunnel on Vassar Street in Cambridge. As the main MIT campus did not move to Cambridge from Boston until 1916, the wind tunnel preceded the “new MIT” by two years. The wind tunnel and wind tunnel tests formed the basis for a graduate course in aeronautical engineering in the Department of Naval Architecture and Marine Engineering until 1920.
In 1917, following the entrance of the United States into World War I, the U.S. War Department leased the wind tunnel. Among the engineers assigned to the wind tunnel were Edward P. Warner, Shatswell Ober, and John R. Markham. Ober and Markham remained involved with MIT’s wind tunnels until 1960. In 1921 the lease agreement was terminated, although the Air Service continued to support wind tunnel testing at MIT with annual grants until 1926.
The increased size and speed of airplanes during the 1920s and 1930s required building a larger, more effective wind tunnel. By the fall of 1933, several tunnels were available for instruction and development testing. Hunsaker was named to head the Department of Mechanical Engineering and placed in charge of its “course” in aeronautical engineering. A significant step towards a new and substantial tunnel was made in 1935 upon the crystallization of a design. The new tunnel would be a closed single return circuit with a secure elliptical operating test section 7.5 by 10 feet, enclosed within an outer steel shell that would allow pressurized tunnel operations and thus achieve a variable Reynolds number capability. The driver was a 2,000-horsepower pole-changing induction motor and controllable pitch 13-foot diameter fan. Measurements of forces and moments over adjustable pitch and yaw ranges were made with a rigid pyramidal support balance with remotely indicating, self-balancing mechanical beams.
The MIT Corporation received a proposal for the construction of the Wright Brothers Wind Tunnel in 1936 and approved it the following year. The MIT Corporation, airplane manufacturers, friends of Wilbur Wright, and other interested individuals provided approximately $230,000 in funding. During the early years of its operation, the Wright Brothers Wind Tunnel was used extensively by the aircraft manufacturing industry to test scale models of their latest aircraft. In 1940, with the addition of equipment donated by the Curtiss-Wright and United Aircraft Corporations, it became possible to test for the aerodynamic characteristics of powered models, a significant advance that produced more accurate test results. During World War II, the tunnel was used 24 hours a day to test military airplanes designed by commercial manufacturers for the allied war effort. Shatswell Ober, Joseph Bicknell, and John R. Markham supervised the organization of a formal Wright Brothers Wind Tunnel staff consisting of project engineers and shift leaders to meet the needs of continuous operation.
The 7.5-foot wind tunnel, made obsolete by the Wright Brothers Wind Tunnel, was dismantled in 1941, and the 4-foot wind tunnel was used sparingly. In 1948 the five-foot wind tunnel, which used too much power and took up too much space, closed. Simultaneously, students in course 16.62 (Aerodynamic Laboratory) were required to perform one laboratory exercise using the Wright Brothers Wind Tunnel. Staff designed and built a new student wind tunnel to free up the main tunnel for commercial research. The new student wind tunnel, constructed in 1948 and used until 1961, had a 4.5-foot by 6-foot diameter test section, a six-component aerodynamic balance, and special equipment for testing powered models.
In the late 1960s, the administration sought to broaden the match of the tunnel’s capabilities to meet the needs of the civil engineering and architectural communities. Beginning in 1972, the facility took on the major undertaking of using wind tunnel simulations and onsite measurements to explain the infamous window failures in the then-new John Hancock Tower in Boston. In the late 1970s, a design evaluation assignment was awarded to establish the wind effects on the facade and at ground level for the Sears Tower in Chicago. The Wright Brothers Wind Tunnel hosted several other ground studies (radome housings, the Battery Park and World Trade Center Towers area at the southern tip of Manhattan, antenna configurations, galloping power transmission lines, and tall structures in Cincinnati, Columbus, Orlando, Toledo, and Boston.)
Each semester, the MIT School of Architecture conducted special lectures and demonstrations of wind tunnel practice. The presence of graduate Research Assistants from Civil Engineering became a regular feature, and the Mechanical Engineering Department conducted studies on smokestack plume pollution, helicopter rotors, a gust-generating system for general wind tunnel applications, and acoustical sensing.
In 1979, as interest in aeronautics increased, a growth in airplane testing took place alongside the ongoing industrial studies. The Fairchild Republic Company became a major user of the facility. It successively developed several aircraft, including the Saab/Fairchild SF340 twin-engine transport, the USAF T46A Next Generation Trainer, a drone vehicle, a forward-swept wing fighter prototype, and several advanced preliminary design configurations. The Digital Equipment Corporation provided a new computation system for automated data acquisition. Thanks to special support grants from Fairchild, the facility acquired a new test control console, which was a complete reconfiguration of the original balance system allowing the installation of modern strain gage sensors for all six components, computation system peripherals, and encouragement to pursue recertification for pressurized operations with either air or a heavy gas. In 1984, during development testing of a joint Boeing/Fairchild model, pressure operations over the range from 0.5 to 1.5 atmospheres were carried out for the first time in three decades to examine Reynolds number effects, and the maximum pressure has since been extended to 2.0 atmospheres.
In recent years, faculty research interests generated long-range studies of unsteady airfoil flow fields, jet engine inlet-vortex behavior, aeroelastic tests of unducted propeller fans, and panel methods for tunnel wall interaction effects. Industrial testing has included auxiliary propulsion burner units, helicopter antenna pods, in-flight trailing cables, new concepts for roofing attachments, a variety of stationary and vehicle-mounted ground antenna configurations, and the aeroelastic dynamics of airport control tower configurations for the Federal Aviation Authority. The tunnel has also been used for live tests in Olympic ski gear, astronauts’ space suits for tare evaluations related to underwater simulations of weightless space activity, racing bicycles, subway station entrances, and Olympic rowing shells for oarlock system drag comparisons.